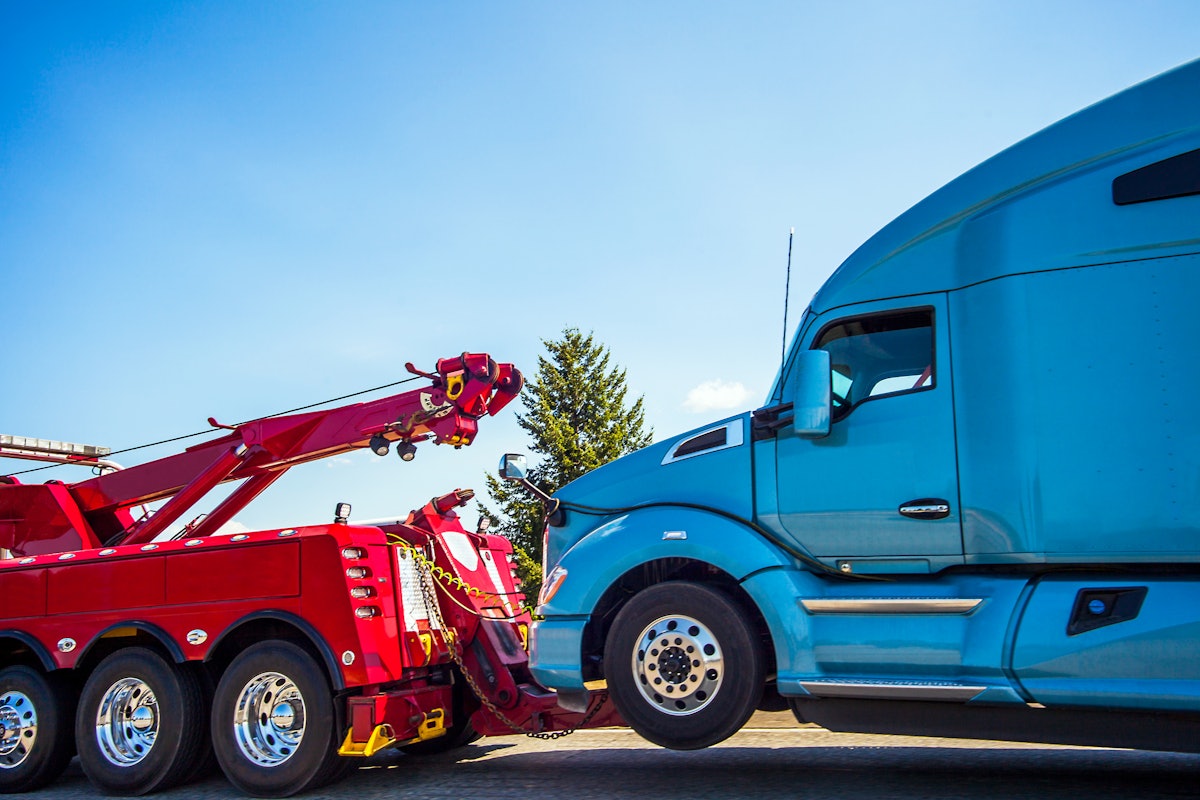
Vehicle recalls are, sadly, in the news weekly. In the “good old days” of my youth, I cannot remember once having a recall on any of my parent’s cars. I suspect those ubiquitous station wagons were designed to be impervious to recalls, and that contributed to their market demise as all the other vehicle types were jealous. Or maybe the pre-civilized world without smart phones or internet meant we never got the notices.
As a mechanical engineer, I concede that the software people have won the market branding war. It started when the 1960s defense and space program term “systems engineer” was co-opted in the 1980s and 1990s into “systems engineering,” meaning solely computer software and hardware.
As a recovering aerospace systems engineer responsible for complete vehicles, I have long taken exception to branding “systems” as only consisting of software and computers, but, alas, that is shouting into the abyss. The greatest understatement I’ve heard in multiple programs over my years always starts with “it’s only software.”
While I will concede on simplistically defining systems engineering, I will not give ground on the faulty assumption and market branding that software updates can fix everything.
I was reading about a Ford recall of more than 550,000 pickups to address the possibility that the transmission might downshift unexpectedly. The immediate solution is for owners to bring their trucks in to “a local Ford dealership, where staff will update the PCM software.” This apparently cannot be accomplished via over-the-air updates (OTA). Topping that inconvenience is that “corrosion” or “faulty connector pins” may be part of the root cause. To the best of my admittedly limited engineering knowledge, corrosion cannot be fixed by a software update. But maybe that’s just my inexperience.
Then there is a recall from Mack concerning a potential faulty high-voltage electrical connector on their medium-duty vehicles. The cable may become loose. Owners are advised not to drive their vehicles and to take them into a dealership for inspection and repair. Notification letters may come out in August. Inconvenience aside, to Mack’s credit, none of the announcements I read said anything about software updates being required.
Paccar announced a recall of 3,887 vehicles covering multiple Peterbilt and Kenworth vehicles for a potential issue with steering from an improperly heat treated mechanical part. Again, operators are to bring the vehicle into a dealership for inspection and possible repair, with notices to be sent in August. Operators are advised not to drive the vehicles until this occurs. Again, while inconvenient, to Paccar’s credit, none of the announcements I read indicate a software update is required.
Tesla announced a recall of nearly 120,000 vehicles for doors that may accidentally open during travel. The solution was an OTA update issued for all the affected vehicles. They also announced a recall affecting Cybertrucks related to trunk bed trim and another related to wipers, but these particular issues will require physical fixes so the vehicles will need to be touched by service people.
All these examples highlight some key realities of vehicle ownership.
1. Nearly all vehicles are imperfect.
2. OEMs have warranties because things break in the real world.
3. The real world is increasingly responsible for proof-testing vehicle designs.
4. Physically touching a vehicle always will be needed to inspect and repair it.
That last one is a message to the Artificial Intelligence (AI) advocacy group that believes computers don’t make mistakes and all issues can be fixed by computer updates. I’ve worked with top corporate software developers and information technology professionals, and I can tell you they were kept busy doing maintenance of hardware and software. The work ranged from simple component failures to massive system incompatibility issues linked to software updates. For example, try putting a new operating system on a 10-year-old computer. The real world has 10-year-old computers and sometimes ones that are much older.
My fourth example should encourage technicians that there is plenty of work in the future servicing real-world vehicles. The challenge will be staying on top of the rapidly changing technologies. The AI gurus will help with staying up to date, offering ever improving automated troubleshooting guides. The vehicles will get increasingly more sensors to help the AIs with this, which brings me to a fifth finding.
5. Sensors fail in the real world.
More sensors typically mean more cost, more complexity, and, importantly, more failure points. False positives and false negatives are going to be a bigger part of the troubleshooting experience. Is the truck broken or is the sensor giving poor data? Combinations of failure modes that were never envisioned by the engineers occur in the real world. Is a failure intermittent or complete?
Every apocalyptic automated future transportation universe requires maintenance people. The fundamental truth is that the more capable the maintenance people, the quicker the vehicles get back on the road.
Technicians and dealers take heart. There will be a future for you when all us “bored, repetitive task” workers like artists, writers, factory workers, drivers, fleet owners, warehouse owners, mechanical engineers, software engineers, freight brokers, shippers, etc. are replaced by AI.
Rick Mihelic is NACFE’s Director of Emerging Technologies. He has authored for NACFE four Guidance Reports on electric and alternative fuel medium- and heavy-duty trucks and several Confidence Reports on Determining Efficiency, Tractor and Trailer Aerodynamics, Two Truck Platooning, and authored special studies on Regional Haul, Defining Production and Intentional Pairing of tractor trailers.