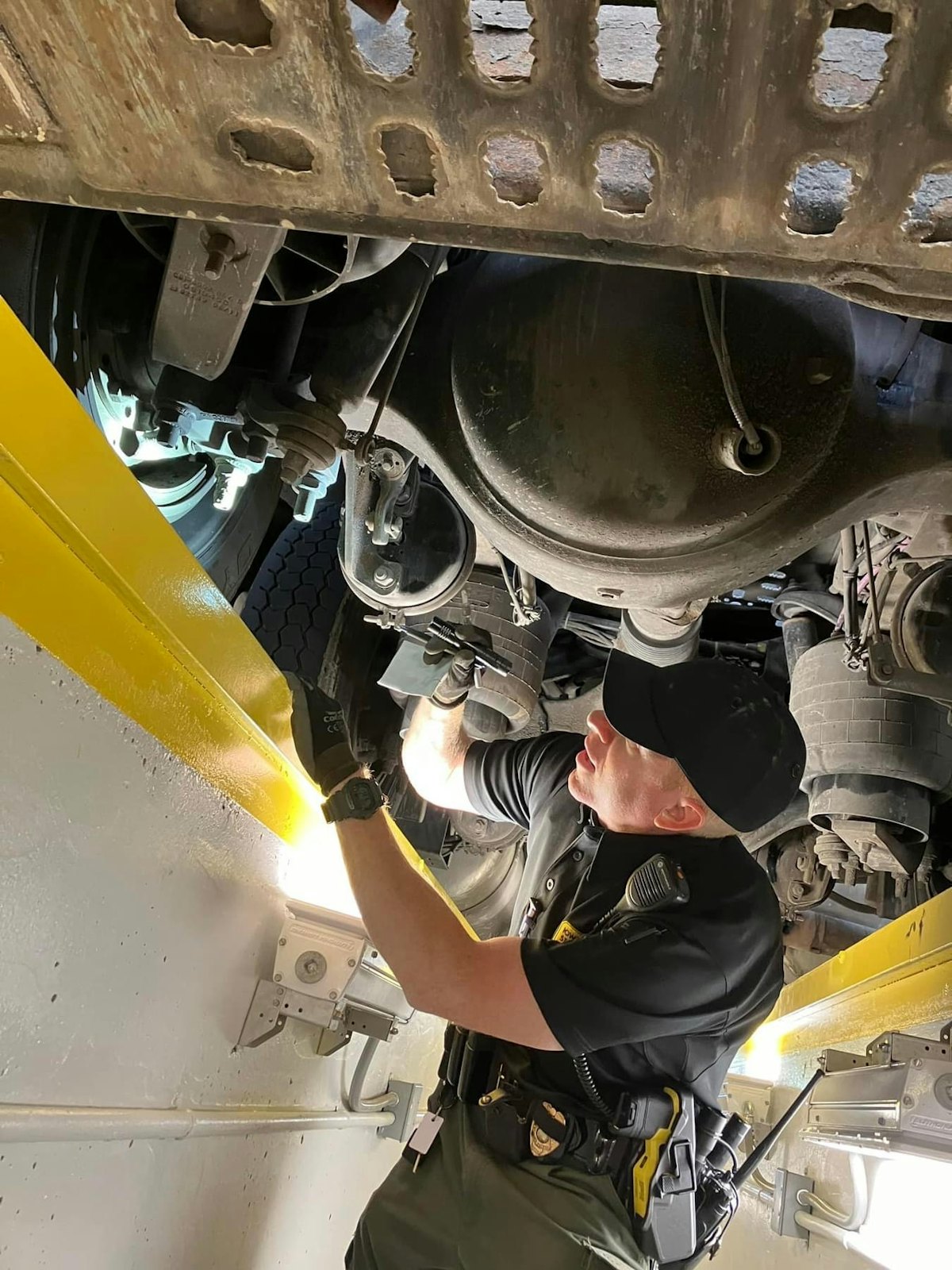
The amount of power a tractor has to get its 80,000 pound limit up to speed is a prideful discussion among drivers at the truck stop lunch counter. The truck’s ability to safely come to a stop, however, is rarely debated with the same passion.
Brake systems have been the top out-of-service violation during the Commercial Vehicle Safety Alliance’s annual Roadcheck campaign dating back to at least 2017. Brake-related violations accounted for six of the top 20 vehicle violations last year.
Making adjustments
“One thing I see constantly is a general lack of knowledge of how an S-Cam brake works with automatic slack adjusters,” noted Brian Screeton, manager of technical training & service for Bendix Commercial Vehicle Systems. “Technicians, perhaps because they are told to do so or this is how they were taught, will tighten up the slack and then back it off a half- or quarter-turn and call it good. If this is done, the technician has no idea of how the brake is working.”
[Related: How to ensure brakes pass DOT roadside inspection]
All brake inspections should start with measuring brake stroke, Screeton added. Measuring stroke, in addition to a thorough visual inspection, is how a technician can determine if the brake is working properly. A longstanding Bendix Technical Bulletin (TCH-005-014) – available at Bendix’s online document library – provides details and tips on the inherent dangers of manually adjusting an automatic slack adjuster to correct out-of-adjustment brakes.
One of the top root causes within brake system violations is over stroke, often caused by worn S-Cam bushings that are either not identified early enough or not being replaced during a brake job, noted Denisse Pedraza, Haldex product line director for brake systems (Americas).
“If a brake is found to be out of adjustment, don’t just re-adjust it,” added Warren Smith, a diesel technician with Ryder and the 2024 Ryder Top Tech champion. “Find the root cause as to why it became out of adjustment.”
While pre-trip inspections can help identify and address these problems early, Pedraza said the underlying causes typically are improper shoe-to-drum fit, either during new installation or replacement cycles. When the shoe is not correctly centered, it directly interferes with having the proper adjustment.
Brake Safety Week
During Brake Safety Week last year, 330 vehicles were issued a “20% violation,” a violation that occurs when 20% or more of a vehicle’s service brakes are out of service and defective. Brake Safety Week is an annual campaign by the Commercial Vehicle Safety Alliance (CVSA) that takes place during a week in August to focus on commercial motor vehicle (CMV) brake safety. The nationwide blitz this year will be held Aug. 25-31.
During the campaign, CVSA-certified inspectors conduct roadside inspections and remove CMVs with OOS brake violations from the road until they are fixed. The goal of Brake Safety Week is to reduce the number of crashes caused by faulty brakes by educating drivers, technicians and others on proper brake maintenance and operation. Brake Safety Week this year focuses on the condition of the brake lining and pad.
On steer axle brakes, the lining/pad thickness should not be less than 4.8 mm (3/16″) at the shoe center for a shoe with a continuous strip of lining; less than 6.4 mm (1/4″) at the shoe center for a shoe with two pads; or worn to the wear indicator if the lining is so marked for air drum brakes, according to Federal Motor Carrier Safety Administration (FMCSA) guidelines. The steering axle brake lining/pad thickness shall not be less than 3.2 mm (1/8″) for air disc brakes or 1.6 mm (1/16″) or less for hydraulic disc, drum and electric brakes.
On non-steer axle brakes, CVSA requires a minimum brake lining/pad thickness of 6.4 mm (1/4 inch) or to the wear indicator if the lining is so marked (measured at the shoe center for drum brakes); or less than 3.2 mm (1/8″) for disc brakes. Hydraulic or electric braked commercial motor vehicles should not be operated with a lining/pad thickness less than 1.6 mm (1/16″) measured at the shoe center for disc or drum brakes.
“Additionally, failing to replace brake lining material when it is below minimum thickness during a brake job can also be an important root cause of OOS violations,” Pedraza said.
When performing a brake shoe replacement, Smith suggested always using all included hardware, removing seized anchor pins and installing new pins lubricated with EP-2 grease to prevent seizing.
Weren’t air disc brakes supposed to stop brake violations?
Looking at the actual number of brake violations going back the last few years with enforcement campaigns, the number of violations doesn’t change a lot. Disc brakes are increasingly more popular, and from a maintenance perspective those are simpler to maintain than drum brakes. Their simplistic nature, Screeton said, often breeds complacency.
“Most of the time, air disc brakes do not get the in-depth inspection that a drum brake does because there is simply not much to see. Inspectors can look for things like rusty brake rotors (an indication the brake is not working), missing fasteners, drop hoses, etc,” he said. “But with modern air disc brakes, the ability to inspect roadside is limited.”
That is not the case for regular preventive maintenance inspections, Screeton noted, where the air disc brake can be thoroughly examined at a set cadence to catch anything that could potentially be wrong early. “This lack of inspections, or the improper suggestion that air disc brakes do not require regularly scheduled inspections as part of a fleet’s maintenance schedule, could also open the door to possible issues that may contribute to violations during roadside checks,” he added.
While disc brakes are easier to maintain and allow for quicker maintenance, Pedraza said this can sometimes lead to issues being overlooked during routine inspections, contributing to the steady number of violations.
“The design of disc brakes and calipers also represents challenges for simple visual inspection; however, Haldex ModulT addresses this by offering a visual inspection feature that allows you to check pad wear without removing the wheel, making the pre-trip inspections easier, efficient and effective,” she said.
Justin McCoy, Cummins Drivetrain and Braking Systems senior product manager, said roughly 80% of the current truck and trailer fleet still uses drum brakes, “so the overall impact of disc brakes on citation rates will initially be small.”
“A significant portion of trailers in particular are still equipped with drum brakes. Does the CVSA out-of-service (OOS) criteria differentiate between truck and trailer brake violations? It would be insightful to examine the specific types of violations being recorded. For instance, with disc brakes, the adjuster is internal to the caliper, so “brake out of adjustment” violations should be less frequent,” he said. “However, issues like air hose and brake chamber defects are likely occurring at similar rates across both drum and disc brake systems. Looking at the data, the percentage of vehicle OOS violations has been steadily declining, though there was an increase following the pandemic. During the pandemic, empty roads may have led to increased speeding and risky driving, which remains a concern. This may have also affected vehicle maintenance. Notably, vehicle inspections dropped by nearly half during the pandemic and still haven’t returned to pre-pandemic levels. This reduction in inspections may have contributed to the trends we’re seeing in OOS violations.”
Brake blocking and tackling
To make sure the brake system is up to the stresses it will face on the highway, Screeton said the best thing fleets can do is make sure maintenance personnel are well-trained as part of an ongoing educational program “and have the knowledge needed to do a proper brake inspection to catch any issues before it becomes an issue on the road.”
“There are three keys — best practices – to have in place,” he added. “First, ensure your maintenance team is measuring brake stroke on drum brakes on every PM or brake inspection. Next, make sure drivers know what they are looking for on their pre-trip inspections and what actions to take based on their findings. And, finally, ensure your technicians are properly trained on air disc brakes, including how to inspect the disc brake per the manufacturer’s service information for that brake.”
Smith further recommended that fleets not simply replace the shoes with what came off the unit, rather check that the proper shoes are being installed by checking the manufacturer specs for proper shoe replacement.
“When performing brake repairs, be sure to inspect wheel bearing condition and end play, especially on trailers,” added Ben Cheaney, of Ryder’s Evansville, Indiana, shop and Ryder Top Tech third place winner. “Remember, these vehicles use the same roads as your family.”
A primary cause of brake-related out-of-service violations is often due to not conducting thorough inspections and maintenance of the entire braking system, noted Steve Edie, senior product manager – air brake, air systems & MTIS for Cummins Drivetrain and Braking Systems.
“Fleets may focus on the problem at hand, replacing specific components such as brake shoes, but overlook the inspection and maintenance of other critical parts like camshafts, cam kits, and slack adjusters,” he said. “While regular maintenance incurs costs, it is significantly more economical than addressing the repercussions of brake failure or out-of-service violations. Proper brake maintenance reduces the risk of unexpected breakdowns, ensuring vehicle uptime and uninterrupted business operations.
Other potential causes may be the qualification level of the technician doing the inspection, Edie said, or lack of communication from the driver regarding noticeable issues such as abnormal sounds when braking. “Additionally, the quality of brake components directly impacts overall vehicle performance,” he said. “Fleets should prioritize using high-quality parts to enhance both efficiency and safety.”
When performing brake maintenance, Edie said it’s essential to inspect and maintain the entire braking system. While the wheel end is already open, go ahead and inspect the rest of the brake system.
“The objective isn’t to increase the number of brake jobs, but to ensure that each one is complete, resulting in more uptime for the fleet,” he said. “We’ve developed a recommended service ratio that addresses four out of the top 5 brake components most responsible for out-of-service (OOS) violations. Fleet operators can use our Complete Brake Job calculator tool on MeritorPartsXpress.com to generate a customized report, comparing their current maintenance practices against our recommended ratios. Additionally, we offer tech tips for critical brake components and training modules through Meritor BullPen to guide comprehensive brake jobs. With each brake they touch, the technician must ensure that the vehicle leave the service center in the best operating condition possible.”