Bringing an all-new truck to market isn’t just an exciting proposition for the truck designers. It’s also an opportunity to reevaluate the way everything is done at the plant where that truck will be built.
Mack Trucks did just that at its Lehigh Valley factory where it will build the new Pioneer, but also continue building the Anthem and of course the vocational Granite. Gunnar Brunius, vice-president of Mack’s Lehigh Valley operations, gave industry press a tour of the plant in advance of the Pioneer’s unveiling.
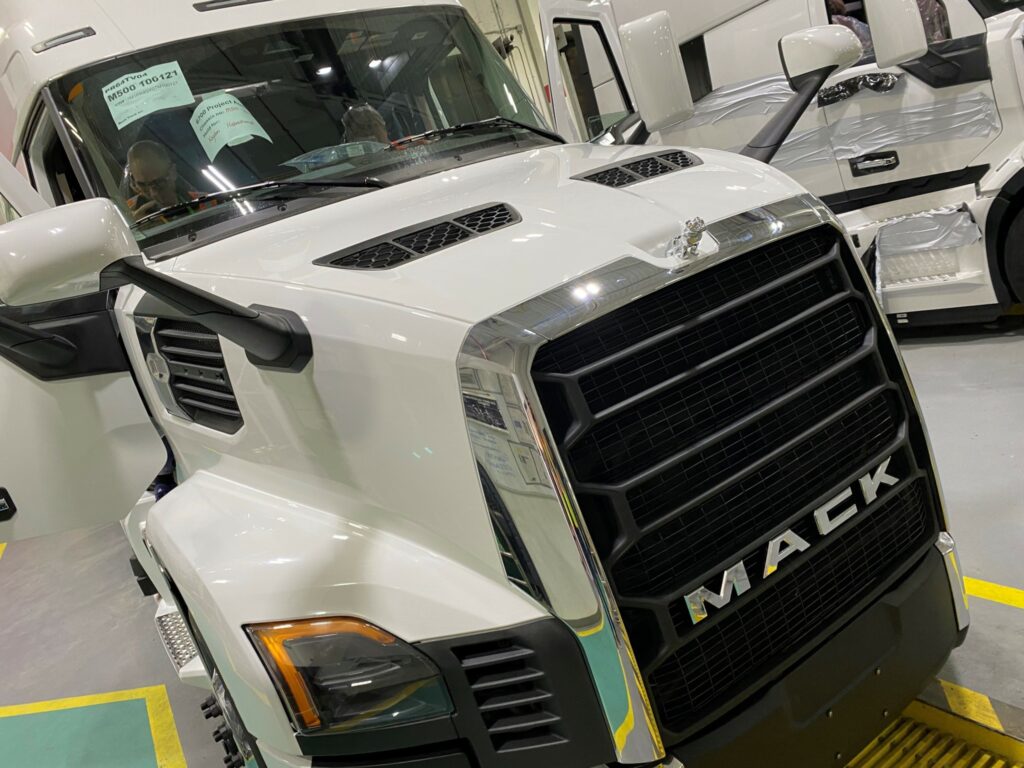
The first prototype Pioneer rolled off the line last October, but preparations were underway much longer.
“I would say that the process for restructuring the whole plant started three-and-a-half years ago,” Brunius said.
The physical retooling of the plant began in the summer of 2023. The goal was to not only retool the line to build Mack’s new flagship highway truck, but to extend those improvements to other models built there.
Plant enhancements were also made with the workers in mind; improvements were made to ergonomics, and automation now takes on more of the heavy lifting that can lead to injuries.
Brunius noted previous highway models introduced over the past 25 years were built upon the Pinnacle platform. The Pioneer, on the other hand, features an all-new body-and-white and is 90% redesigned from the ground up.
That generated excitement at the plant where the truck will be built. “We have been doing lots of facelifts, but this is from scratch,” said Brunius. “We have redesigned the whole product, the way we build the cab, the way we build the chassis, is totally different than with the legacy products.”
The focus for the plant updates was on employee safety, product quality, and product quality. No, that’s not a typo. Brunius said beyond safety, the focus was entirely on quality. This was especially important given the advanced technologies that go into the newest highway trucks; Brunius noted there are 36 electronic control units (ECUs) on the Pioneer, up from eight to 10 on legacy models.
It’s also the first Mack to feature a 24-volt electrical architecture. “It’s a rolling computer,” said Brunius.
Redesigning the plant meant going from station to station, looking for any areas where improvements could be made or efficiencies gained. “Wherever we could find an opportunity to merge the processes, we have merged them,” Brunius said.
Examples include building more modular battery box and dash units that can be more easily and efficiently inserted into the truck on the line. More than 15,000 part numbers now have new homes in the plant to further drive efficiencies. It was a US$175-million investment for Mack, with an end goal of improving employee safety and productivity while also churning out trucks to unprecedented quality standards.